5 Steps to Properly Restacking and Reworking Pallets
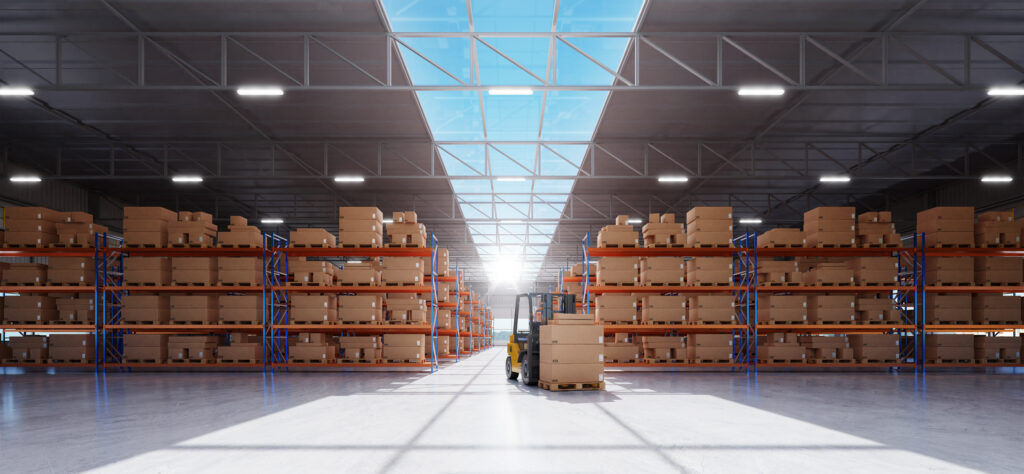
Introduction
As a freight broker, you’ve likely seen a pallet tip over at some point. It’s one of the most common problems in the industry, and it can cause costly delays and damaged merchandise. A tipped-over pallet isn’t just a nuisance, it’s a sign that something went wrong during the loading, stacking process or delivery driver.
The good news is that you can take steps to prevent this from happening. In this blog post, we’ll outline the TOP 5 steps for properly restacking and reworking pallets. These steps are crucial to creating a strong foundation for your freight and ensuring it gets delivered on time and in good condition. So, let’s get into the five steps to properly restacking and reworking pallets.
Step 1: Ensure You Have the Right Type of Pallet
Before you even begin restacking, it’s crucial to have the right foundation: the right pallet. You’ll want to make sure you’re using the same type of pallet that was originally used for the shipment. This means checking for any damage, like broken boards or loose nails.
Most retailers prefer nine-block pallets from companies like CHEP or PECO. These pallets are built to handle heavier loads and stack more securely. Having a stash of these pallets in your warehouse is a great way to be prepared when a shipment arrives.
If you don’t have the correct pallets on hand, you can often get them from your supplier or a local pallet supplier.
Step 2: Understand the Stacking Pattern
Once you have the right pallets, it’s time to pay attention to the stacking pattern. Each row on a pallet generally has a unique layout. Before you start restacking, take some time to map out how the boxes were originally arranged. This will ensure that your re-stacked pallet is as stable as the original.
Think of it like a puzzle. You want to recreate the same pattern to ensure the pallet is secure and stable. This offsetting of the boxes helps lock them in place and prevents the pallet from becoming unstable or tipping over.
Step 3: Stacking with Precision
Now it’s time to start building your pallet. As you stack each box, ensure they’re positioned corner-to-corner, forming a tight and even base. Avoid creating an uneven or “bowed out” base – think of it as a foundation for a building, you want it to be solid.
A strong base prevents the pallet from shifting or taking on an uneven shape as it gets taller. This is key to preventing the pallet from tipping over, especially when it’s being moved or transported.
Step 4: Count the Rows
Before you reach for the shrink wrap, take a moment to count the rows on the original pallet. You want to make sure you’re restacking the pallet at the same height as the original.
Why is this important? The shipper chose a specific height for a reason. It could be due to the weight of the merchandise or the stability of the pallet itself. Stacking too high can lead to an unstable pallet that’s prone to tipping over.
Step 5: Secure with Shrink Wrap
You’ve carefully chosen the right pallet, understood the stacking pattern, built a solid base, and counted the rows. Now comes the final step: shrink wrapping. This is the most important part of the process, and it’s where you lock everything in place.
Start by wrapping the bottom row of the pallet at least five times, making sure the wrap is attached to the actual pallet to provide a solid foundation. As you move up the pallet, crisscross the wrap, creating a tight and secure hold on the entire stack. You want to apply enough tension so nothing can move from side to side.
Pro Tip: Invest in the Right Tools
For even tighter and more secure shrink wrapping, consider investing in a hand shrink-wrapping dispenser. These dispensers give you more control over the tension of the wrap, allowing you to create a super-tight wrap that’s less likely to come loose.
The bonus? You’ll use less shrink wrap overall, saving you both money and time.
And for an added dose of safety, we recommend using a long-handled dispenser. This helps protect your staff from back strain and makes the shrink-wrapping process easier on their bodies.
Taking the time to invest in the right tools can make a huge difference in the efficiency and effectiveness of your pallet restacking process.
Conclusion
Restacking and reworking pallets might seem like a simple task, but it’s a crucial step in ensuring the safe and efficient movement of freight. By following these five steps, you’re not just creating a stable pallet but also building a strong foundation for a successful delivery.
Remember, a properly restacked pallet means:
- Reduced risk of tipping: Less chance of delays and damage.
- Enhanced customer satisfaction: Delivering freight on time and in good condition.
- Stronger reputation: Building trust and confidence with your customers.
So, take the time to invest in these practices. It’s a small investment that can lead to big rewards for your business! Find out how WeFixFreight can help.
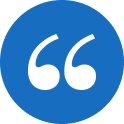